
Welcome to the Site, your ally in Engineering to cover your FEA simulation needs
Get a complete view of your system or structure using our finite element analysis service.
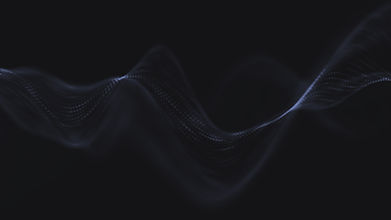
Discover how we can take your project to the next level with our finite element analysis services.
Structural analysis of pipes
Allow our experts in pipe structural behavior analysis to provide you with a deeper understanding of pipe behavior under different initial conditions and how they can benefit your business in decision making.
Variedad de Aplicaciones
Ya sea que necesites análisis generales en el sistema, estamos aquí para proporcionarte soluciones personalizadas que se adaptan a tus necesidades.
Improving data accuracy
Our focus on simulation science with appropriate models such as: RANS, LES, DES,KE, KW, Spalart-Allmaras Model, SST; allows obtaining information more in line with the initial conditions of the project under analysis.
Comprehensive Customer Service
At the Site, we not only offer simulation services, but we also make sure that you receive complete support to meet all your needs.
Services
Finite element analysis (FEA) is a computational technique that allows us to simulate how structures behave under various physical forces. In the case of pipes, it is used to evaluate their structural integrity and predict their response to loads, vibrations, heat and other factors.
Stress and strain analysis
Stress (σ): It is the force applied per unit area in a material. It is measured in pascals (Pa) or megapascals (MPa). The tension can be tensile (stretching) or compression (compression).
Strain (ε): It is the relative change in length or shape of a material due to applied stress. It is expressed as a fraction or percentage. The deformation can be elastic (reversible) or plastic (permanent).
Fatigue analysis
Fatigue analysis in structures is a tool that evaluates the validity of the design or its durability under cyclic loading conditions. It is applied to components subjected to repeated loading, such as rotating machines, aircraft wings, railway wheels and bridges. Fatigue occurs gradually due to loading and unloading cycles, weakening parts over time. Fatigue analysis helps predict service life and detect potential cracks before fracture
Thermal analysis
Thermal analysis in structures is essential to ensure that materials and components can withstand temperature variations without failure.
Vibration analysis
Piping vibration analysis involves assessing the movement and stress of pipes to prevent failures caused by vibration-induced fatigue. During design, experts evaluate potential risks, and high-risk areas are tested during operations. Approximately 21% of hydrocarbon releases are due to vibration-induced fatigue failures
Fluid Structure Interaction Analysis
Fluid-structure interaction in piping systems (FSI) involves the transfer of momentum and forces between the pipe and the contained liquid during unsteady flow.
In practical terms, this phenomenon is essential for analyzing pipelines in various engineering applications, such as water, steam, oil, and gas transport.
Modal Analysis
Meaning of Modal Analysis: It’s a technique to study the dynamic characteristics of structures and systems. It provides insights into how these entities respond to external forces or vibrations.
Importance of Modal Analysis: It helps prevent resonance, optimize designs, improve product performance, and ensure safety and reliability in engineering applications.